Estimated read time: 1-2 minutes
This archived news story is available only for your personal, non-commercial use. Information in the story may be outdated or superseded by additional information. Reading or replaying the story in its archived form does not constitute a republication of the story.
OGDEN — Airmen at Hill Air Force Base are going high-tech in hopes of keeping America’s most advanced fighter aircraft in the air, and hoping to save some money along the way.
To help keep the F-35s in the air, the 388th Maintenance Group and Enhancement Program has turned to 3D printing.
The printer makes grommets, fasteners, housing boxes and cable splinters for the F-35 — and it’s all made out of composite plastics and carbon fiber.
Tech Sgt. Scott Mathews, assistant manager of the 388th Maintenance Groups Air Force Repair and Enhancement program said, “With this printer, we’re capable of printing all the way down to a 10 micron layer, which is insanely thin.”
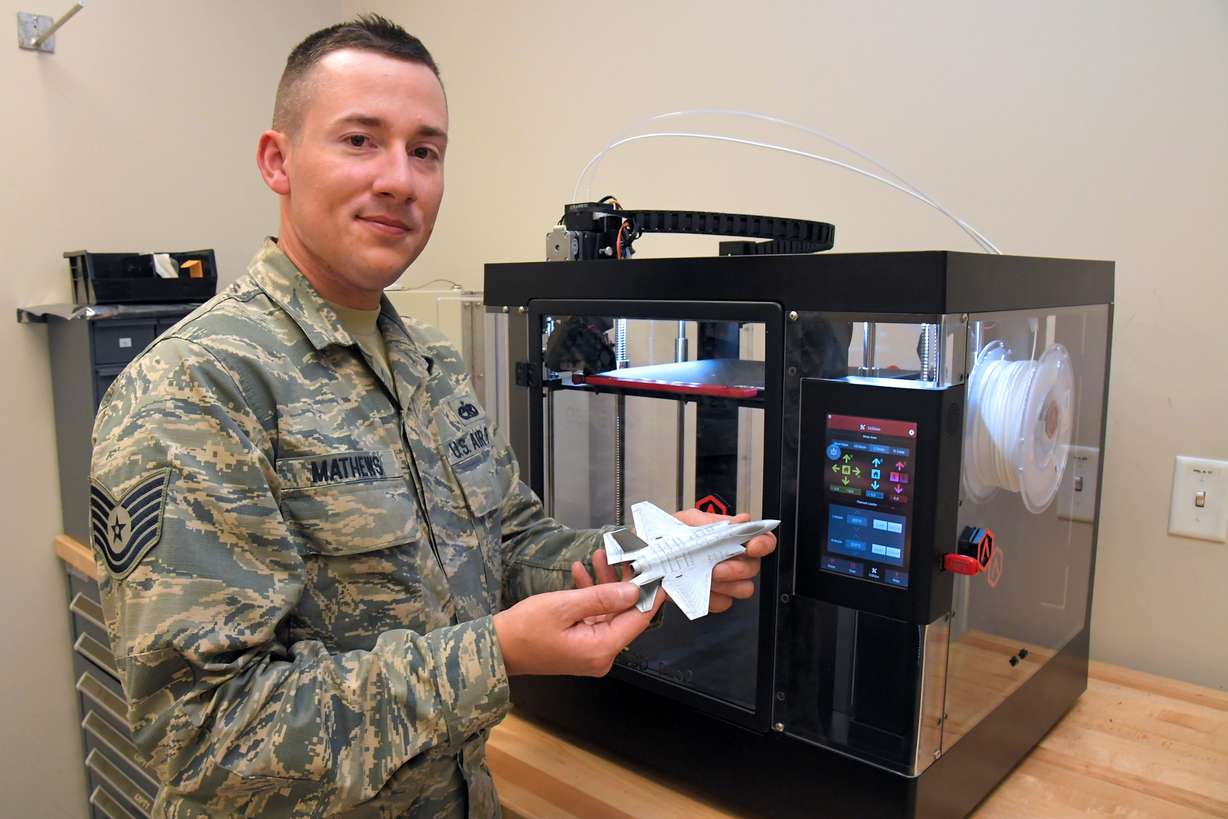
Hill Air Force Base recently acquired the printer with the hope of getting parts faster and driving down costs for replacement parts.
“Especially when you start looking at all of the pieces, parts of getting it from the initial manufacturer, through to the end consumer, the eventual cost of that ends of being exponential,” said Mathews. Possibly thousands of dollars could be saved.
Mathews also said, “When you look at all the different parts you can manufacture, once we get the approval and the go-ahead to actually really start ramping things up, oh, it just boggles the mind of the things we could manufacture.”
Every new part will need to be tested, proven and approved to ensure quality and safety before being put to use.
Mathews said it's like getting paid to tinker around in the garage, “There’s that sense of pride, knowing that you played at least a minuscule role in getting those airborne and keeping them airborne.”